Raw Materials
What Are Raw Materials?
Raw materials are materials or materials that are used in the primary production or manufacturing of goods. Raw materials are items that are bought and sold at the exchange of goods worldwide. Traders buy and sell raw material which is called factor market because raw materials are factors of production such as labor and capital.
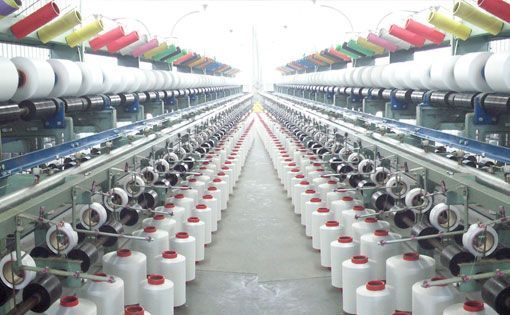
Raw material interpretation
Raw materials are used in many products. They can take many different forms. The kind of raw material inventory a company needs will depend on the type of manufacturing. For construction companies, detailed budgeting in raw material inventories and accounting on the balance sheet and income statement requires a special framework.
Accounting Basics
Manufacturing companies take special steps to list raw materials. It includes three different inventory classifications on their balance sheets, compared to just one for non-manufacturers. The balance sheet's current assets portion for manufacturing companies will include
- Raw materials inventory
- Work-in-process
- Finished goods
When a company uses raw material inventory in production, it transfers them from raw material inventory to work-in-process inventory. When a company completes its work-in-process item, it adds the finished items to the finished goods list, making them ready for sale.
Direct and Indirect Raw Materials
In some cases, raw materials can be divided into two categories: direct and indirect. Whether a raw material is direct or indirect will affect where it is stated on the balance sheet and how it is spent on the income statement.
Direct raw materials are materials that companies use directly in the manufacture of a finished product, such as wood for a chair. Indirect raw materials are not part of the final product, but are instead largely used in the production process.
Indirect raw materials will be recorded as long-time assets. Within long-term assets, they can fall under several different categories, including sales, general and administrative or property, plant and equipment. Long-term assets typically follow some depreciation schedule that expels assets over time and coincides with the revenue they help to produce. For indirect raw materials, depreciation time will generally be shorter than for other long-term assets, such as an extension of a building over several years.
As discussed above, the current assets retain direct raw materials. Direct raw materials are spent on the income statement within the cost of goods sold. Manufacturing companies should take additional steps on non-manufacturing companies to create more detailed expense reporting on cost of goods sold. Direct raw materials are usually considered variable costs because the amount used depends on the quantity being produced.
Key
- Raw materials are required for primary production or manufacturing of goods.
- The price of the direct raw material appears as a current asset on the inventory sheet.
- Africa, the Middle East and China have the world's largest supply of natural resources as a percentage of GDP.
Comments
Post a Comment